目前,管锥螺纹修复加工过程中的对刀检测方式主要以人工手动检测为主,该方式不但检测效率低,且精度也难以保证。本文针对螺纹对刀检测中存在的难题,提出了一种基于霍尔传感器的螺纹综合测量机测量方法,并设计了配套的测量系统,对比以往的测量方法,该方法具有效率高、成本低、抗干扰能力强等优点,为实现螺纹自动化修复奠定了基础。
首先,在对螺纹综合测量机的螺纹修复对刀原理和霍尔传感器测量原理进行深入研究的基础上,分析了霍尔传感器测量螺纹的原理,并论证了将霍尔旋转位置传感芯片应用于管锥螺纹测量的可行性。之后,根据螺纹实际测量要求,确定了本测量系统的系统方案,完成了单片机的选型及其硬件电路的设计,并根据系统的控制要求,完成了通信系统的程序设计,实现了传感器测量数据的采集与存储。
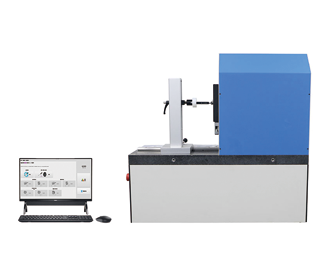
其次,在数控管螺纹修复车床的基础上,搭建了管锥螺纹在机测量实验平台,通过对比实验分析了测量速度、测量方向、测量距离、永磁体的形状和位置等因素对测量数据的影响,根据数据的优劣程度,确定了本实验平台的测量条件。
通过分析现有的数据处理方法,结合螺纹综合测量机螺纹截面廓型测量数据特征,提出了基于窗口数据均值偏差的自适应平滑算法去除噪声干扰,再根据平滑后数据的线性分布规律确定局部拟合窗口宽度,并利用二乘法对窗口数据局部拟合、求取螺纹特征点参数。将算法编入单片机中进行联机调试,通过调试结果与实际计算结果的对比分析,验证了算法程序的正确性,确定了系统的测量精度。
通过在机测量螺纹轴截面廓型,实现螺纹的自动化加工和修复过程,提高螺纹修复加工效率、降低工人劳动强度,使数控螺纹修复车床能够承担更多的螺纹加工和修复任务。